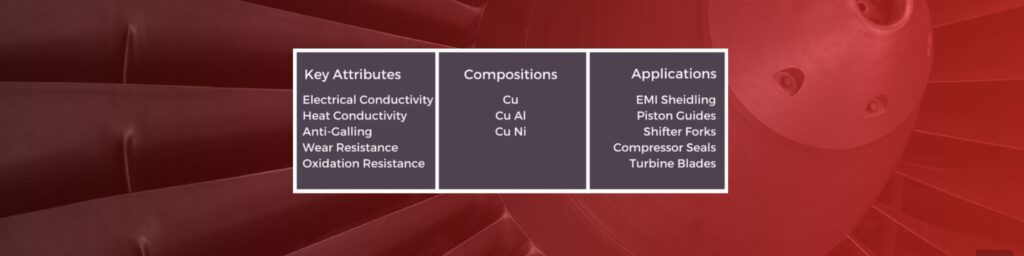
Many engineers will be familiar with Copper through electro-plating. Electro-plated Copper is most often used as a way to create a smooth uniform undercoat for other processes such as Silver Plating. It is thin and malleable in nature and enhances a component with improved electrical and heat conductivity.
The main difference between this and HVOF applied Copper Alloys is that HVOF is an additive process and as such can be built up into a thick coating as well as used to repair worn areas. There are a number of different Copper Alloy based coatings depending on your application.
Copper Coating
Pure Copper Coatings applied through HVOF have similar properties to electro-plated Copper. They provide excellent electrical and thermal conductivity as well as being non-magnetic. HVOF coatings are hard and dense in nature with a low porosity offering greatly enhanced wear resistance against their electro-plated cousin. This coating is often used for EMI Shielding.
Copper Nickel Alloys
Copper-Nickel Alloys are particularly dense in nature and resistant to galling and fretting. These coatings have improved lubricity and are often used in Jet Engine Turbine Blade Roots and Disk Slots due to their excellent thermal properties.
Copper Aluminium Alloys
Copper-Aluminium Alloys are most often used in repair of worn areas in components made of Copper, Brass or even Bronze. They provide enhanced wear and fretting resistance as well as added protection to oxidation when sealed. Typically these coatings are used on pumps as a form of cavitation control, other applications include Piston Guides, Shifter Forks and Compressors.
Quality Assurance
B&B have invested heavily to be able to provide the highest quality of coatings. Our on-site facilities include a CO² climate cooled spray booth and a KUKA robotic arm, both of which enable us to ensure the best possible conditions and control over any coating. We also have an onsite Metallurgical Laboratory for full quality control and reporting.